Flaring and venting of associated gas and low pressure take off gas is literally costing the Earth. When the true cost of this lost product, in terms of the environmental impact and field economics, is included in the field development plans, we should be recovering not disposing of this valuable resource. Export, gas-to-wire and gas reinjection are just some options available for utilising associated gas and replacing flaring in non-emergency situations. These preventable emissions are a major contributor towards the ever-increasing Green House Gas (GHG) problem we all face, with the UK’s Oil & Gas Authority (OGA) recently stating that, for the UK Continental shelf (UKCS) ‘the volume of gas flared and vented in offshore upstream oil and gas production last year (2020) was equivalent to 3% of all the natural gas produced in 2019.’
In the UK, the OGA provides consents for flaring and venting in relation to UK production, and is finally moving to eliminate all but essential flaring and venting. These flaring and venting rates are approximately eleven times higher for the UKCS than for the Norwegian sector, where there has been a ban in place for non-emergency flaring since 1972. Practically, there will always be a need to remove gas inventories in emergencies, however on the UKCS, a large percentage of flaring is due to the disposal of associated gas produced during oil production and, where the economics of a dedicated gas export route are considered financially unrealistic.
But what would the economics look like if a cost per tonne was applied to producers of these E&P associated GHG emissions? Some authorities are pushing for an equivalent cost per tonne for CO2 (figures between $40 and $60 per tonne have been suggested) to be applied to all new field development plans. Meaning that all CO2 emissions from a facility, including fossil fuelled power generation as well as flaring and venting, will carry a tariff. Arguably, operators and designers would then be pushed to include greener alternatives on new facilities, including the adoption of technological solutions such as flare gas recovery and vapour recovery from vent systems. It is worth noting here that some facilities built over 30 years ago often included vent recovery and reinjection systems, but these now sit idle, falling out of favour due to the running costs outweighing the revenue from recovered gas. Now, with the urgent need to reduce GHG emissions and advancement in technology, it’s time to change, especially with the rising importance of gas for hydrogen production. To align with the UK Net Zero vision, the oil and gas sector cannot continue burning off or directly releasing natural gas into the atmosphere.
In attempts to kerb emissions from flaring and venting some national authorities have applied production caps and limits, but this practise does nothing to improve efficiency or apply the practices and available technologies to reduce these emissions, reductions by up to 45% in some estimates. So, tipping our hats to Norway, we need the UK sector of the North Sea to continue with its “Green Evolution” and remove emissions at source, using the world leading technology, much of it British with global export potential. The retrofit of such technologies to existing facilities could carry high costs, but this initiative would make a large contribution to the reduction of GHG’s and thereby gain regulatory support, both at home and abroad. In summary, providing another great opportunity for industry, operators and the UK Government to jointly work towards Net Zero.
TelosNRG are already working with a number of operators to help them understand their GHG emissions and how best to manage and reduce these. Working with the industry to improve efficiency, profitability and reduce the environmental impact and associated costs of their operations. Thereby helping build viable, sustainable and future proof businesses.
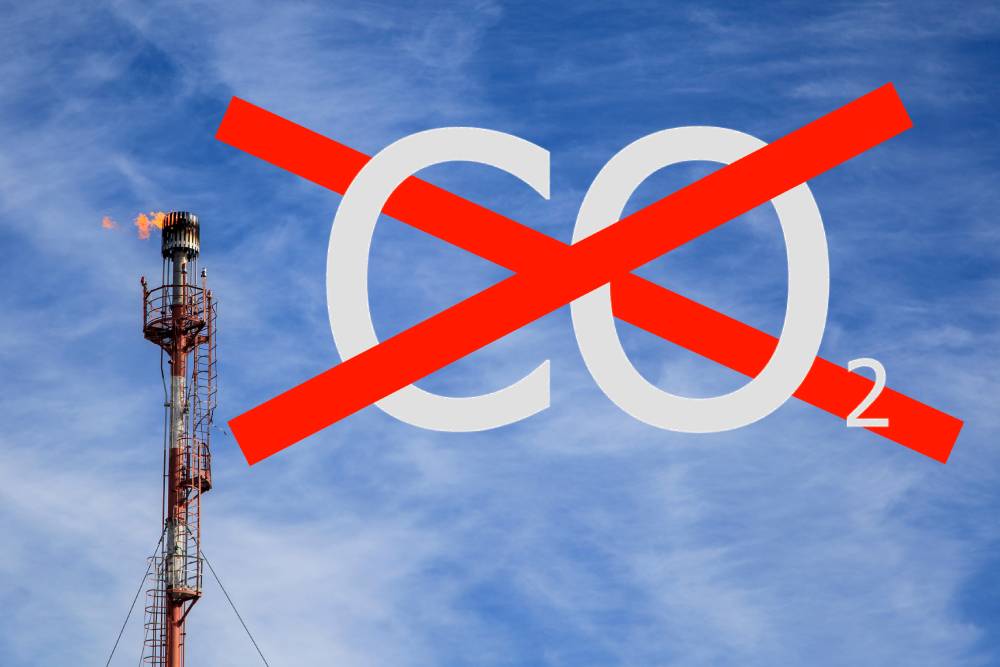